Purification process of high-purity liquefied gases from Repsol
From petroleum distillation, we obtain gas currents that are subject to several selective purification processes, eliminating odours, impurities, and heavy components.
In the first phase, liquefied gases are mixed in the appropriate proportion.
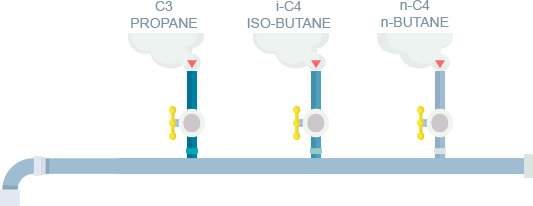
PHASE 1
Catalyst 1
PHASE 2
Catalyst 2

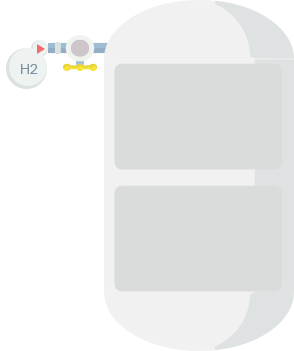

HYDROGENATION (High temperatures and pressures).
Gases are mixed in a bi-catalytic hydrogenation reactor where they are subject to high pressures and temperatures for purification, eliminating olefins and sulphur.
STRIPPING Separation phase.
During the Stripping phase, light compounds, excess H2, and H2S are separated with the help of N2.

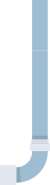
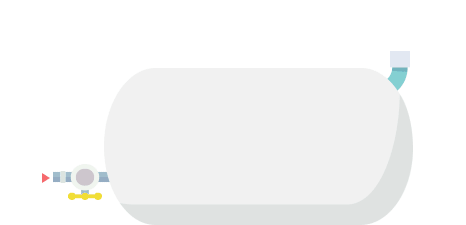

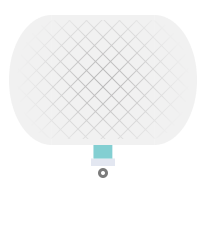
FILTRATION OF HEAVY COMPOUNDS
The remaining gases are subject to a filtration process that extracts heavy compounds and eliminates any residual impurities.
The content of 1,3-butadiene is much lower than the 0.1% required for these products.

FINAL PRODUCT High-purity liquefied gas
Once purified and having the quality required, liquefied gases are stored at room temperature in closed containers and in a liquid phase, thanks to their own vapour pressure, thereby minimising the space they occupy.
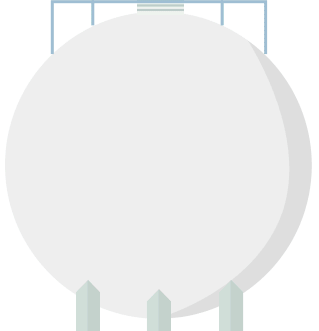
OUR PROPELLANTS:
-
They emit no
unpleasant odours -
They are used as an
alternative to CFCs -
They are eco-friendly and
do not damage the
ozone layer (ODP = 0) -
Their content in
1,3-butadiene is
lower than 0.1% -
Isobutane is suitable
for the food industry
(E-943b) -
Our liquefied gases are exempt
from registration in REACH